![]() |
![]() |
Siemens
![]() |
Safeguards are necessary everywhere where hazards can arise for man and the material being produced. Rotating parts can be a possible source of danger. Usually they are controlled by electrically-operated switching devices. EN 60204/VDE 0113 "Safety of machinery - Electrical equipment of machines, part 1: Specification for general requirements" lays down the safety regulations for electrical controls. It serves primarily to ensure the safety of persons and things, tomaintain functionality and make servicing easier.
Fig. 1 Switching devices for safety circuits e.g. 3SE safety position switch, 3SB emergency-stop control device
Where the norm applies
EN 60204/VDE 0113 part 1 is a basic specification and applies to all equipment with electrical and electronic devices and systems. It also applies to groups of machines which work together in a co-ordinated way. The validity of the norm begins where the device is connected to the mains. EN 60204/VDE 0113 part 1 makes no claims to completeness. Rules and regulations which are laid down in other specifications and norms must be taken into account. These specifications and norms are usually specific to particular machines. EN 60204/VDE 0113 part 1 is not restricted in its use to industrial machines alone. The area of application has been extended considerably compared to EN 60204 part 1: 1985/ VDE 0113 part 1/02.86 (still valid until 01.12.93 for plants still under construction).
Fig.2 3TK28 back-up combination unit
Emergency-stop
Section 9.2.5.4 'Emergency-stop' says that the emergency-stop must function as a category 0 or 1 stop. The user determines the category on the basis of risk assessment. Furthermore, emergency-stop must have priority over other functions. The energy supply to equipment which causes hazardous conditions must be switched off as quickly as possible without giving rise to further danger. This can take place e.g. via mechanical switching-off devices which do not require any external energy supply. For a category 1 stop, reverse current braking can be used. In both categories resetting the emergency-stop device must not initiate restarting. It is important for the construction of the safety circuits to note that for a category 0 stop, only hardwired electromechanical components may be used, and for a category 1 stop, likewise only electromechanical components may be used to switch off the energy supply (see also section 12.3.5 of the norm).
The concept of
risk assessment is explained in the Specification for general requirements (see
EN 60204/VDE 0113 part 1 4.1). "The risks associated with the hazards relevant
to the electrical equipment shall be assessed as part of the overall requirements
for risk assessment of the machine. This will determine the acceptable level
of risk and the necessary protective measures..." "Safety measures are a combination
of measures incorporated at the design stage and those measures required to
be implemented by the user." As the term 'stop function' is used in the 'emergency-stop'
requirements the definition according to EN 60204/VDE 0113 part 1 9.2.2 is explained
below: "There are three categories of stop functions as follows:
- Category 0: stopping by immediate removal of power to the machine actuators
(i.e. an uncontrolled stop ...;" Category 0 is a basic function and applies
for all machines;"
- Category 1: a controlled stop with power to the machine actuators available
to achieve the stop and then removal of power when the stop is achieved;" Category
1 applies for all drives where stopping is achieved as quickly as possible by
electrical and electro- mechanical braking.
"- Category 2: a controlled stop with power left available to the machine actuators
...." Stop functions must take place by de-energizing the corresponding circuit
and they must override related start functions.
Fig.3 3TH4 contactor relay
Safety through redundancy and diversity
As safety circuits must remain fully functional even in the case of a fault, section 9.4 of EN 60204/VDE 0113 part 1 'Control functions in case of failure' must be taken into consideration. Measures to minimise risks are named below, yet are not limited to these alone:- protective devices on the machine itself (e.g. guards),
- protective interlocking of the electrical circuit,
- the use of proven switching techniques and components,
- partial or complete redundancy or diversity,
- functional tests.
Redundancy is when there are more control or drive branches than are necessary to carry out a function. By providing redundancy it is possible to reduce the probability that a single fault in the electrical circuit can produce any danger. In the safety circuits at least 2 switching devices are used for reasons of redundancy. In order to minimise the probability of errors and failures which can lead to hazardous conditions diversity in the functions or through different devices is necessary. In safety circuits this is achieved via the combination of make-contact elements and break-contact elements. Functional tests should also serve to minimise risks. These can be carried out either automatically or by hand via monitoring or testing on starting and after pre-defined intervals. In the circuits described in sections 3, 4 and 5 automatic functional tests are carried out.
Mutual monitoring with 3TH contactor relays
Mutual monitoring with 3TH contactor relays The stipulation of redundancy and diversity in EN 60204/VDE 0113 part 1 is achieved by the working together of three 3TH contactor relays in the safety circuits. For mutual monitoring the circuit is so constructed that the contact elements of the individual contactors are monitored to check that they open and close at every ON and OFF cycle - for example by switching the control voltage on and off with the main switch or by actuating and releasing the emergency-stop device. In the enable circuits, which are used for switching off in cases of danger, the make-contact elements and break- contact elements of the contactor relays are connected in series for reasons of diversity. By activating the safeguard its control voltage is disconnected. In this way cyclic testing of electric circuits for monitoring safeguards takes place.
Switching off Dangers with Contactors in Safety Circuits
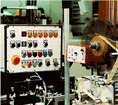
1 Safety imperative
2 The fundamentals of safety equipment
- 2.1 Electric safety circuits according to EN 60204/VDE 0113 part 1
- 2.1.1 Emergency-stop devices in general
- 2.1.2 Emergency-stop circuits with increased reliability
- 2.2 Contractors - Switching devices for electric safety circuits
3 Guaranteed switching off of dangers - the 3TK28 back-up combination unit
- 3.1 Emergency-stop circuit
- 3.2 Monitoring protective devices
- 3.3 Emergency-stop devices for switching off motors
- 3.4 Multiplying the enable circuits
- 3.5 Enable circuits for delayed switching off
4 Suggestions for circuits to build yourself
- 4.1 Emergency-stop circuit: single-branched
- 4.2 Emergency-stop circuit: two branches
- 4.3 Emergency-stop circuit with monitored contactor for switching motors
- 4.4 Emergency-stop circuit with programmable logis controllers
- 4.5 Bringing to a standstill reliably with emergency-stop
- 4.6 Monitoring of movable protective devices
5 Emergency-stop devices according
to DIN VDE 0116:
"Electrical eqipment of firing plants"
- Functions of the emergency-stop circuit: single-branched or with two branches
Crouzet | Seeka-Takex | Proximity Sensors | Brad Harrison | Siemens | Ege I Omron I Erwin Sick I GOSwitch
Home I Suppliers I Price & Availabilty I Newsletters I Sensor Sourcing I New Products I Special Offers I Site Map I Links I Contact